How To Make A Mold For Slip Casting
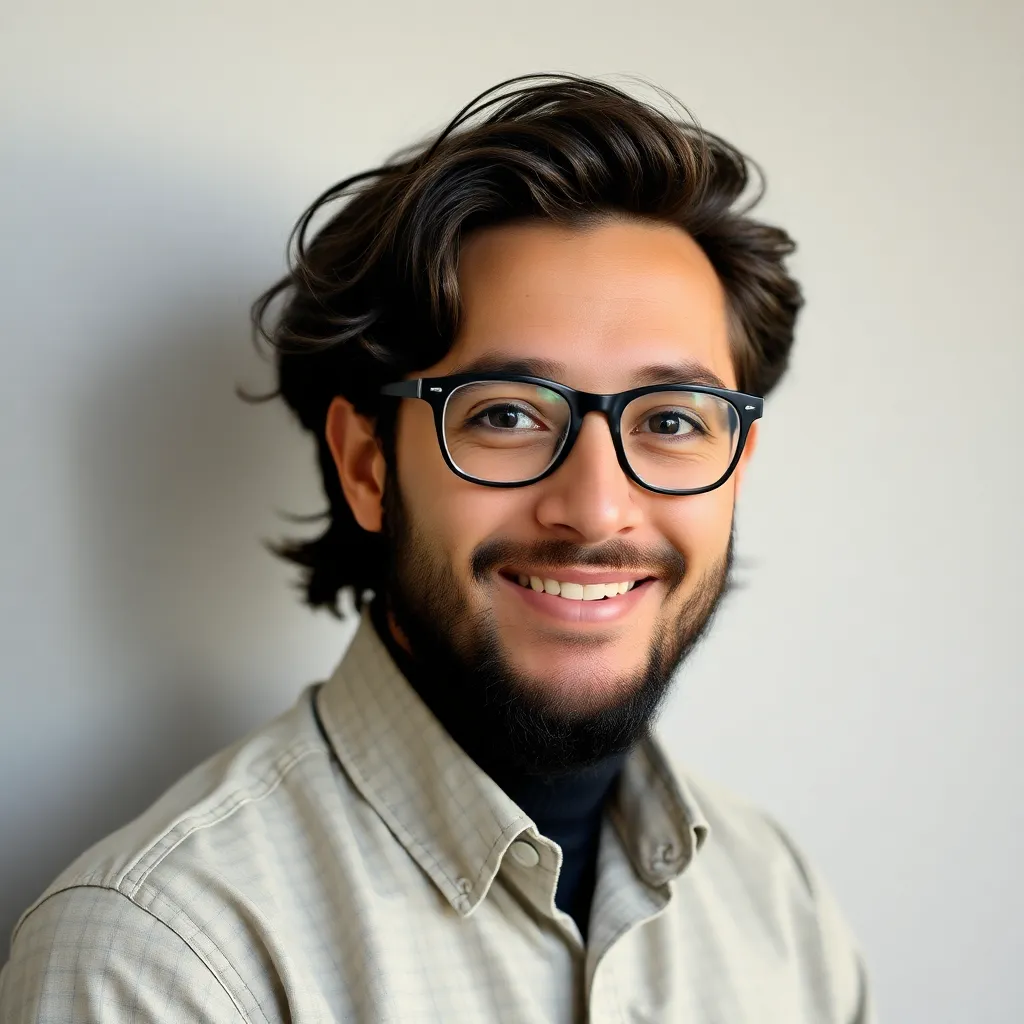
Ronan Farrow
Mar 13, 2025 · 4 min read

Table of Contents
How to Make a Mold for Slip Casting: A Comprehensive Guide
Slip casting is a ceramic process that uses a liquid clay suspension, known as slip, to create hollow or solid forms within a plaster mold. Creating the mold is a crucial first step, and this guide will walk you through the process, offering tips for success.
Understanding Plaster Molds for Slip Casting
Plaster molds are the heart of the slip casting process. They absorb water from the slip, causing it to solidify against the mold's walls. This creates a ceramic shell that mirrors the mold's shape. The type of plaster used is crucial; dental plaster is often preferred for its fine texture and ability to create detailed molds. However, building plaster can also be used for less intricate projects.
Key Properties of Good Plaster Molds:
- Porosity: The mold needs to be porous enough to absorb water quickly and efficiently. This ensures rapid casting.
- Durability: Repeated use requires a sturdy mold that can withstand the stresses of repeated casting and cleaning.
- Accuracy: The mold must accurately reproduce the desired shape and detail of your ceramic piece.
Step-by-Step Guide to Making a Slip Casting Mold
This guide uses a two-piece mold for ease of removal, ideal for many slip-casting projects. Adjust as necessary for single-piece molds (which are suitable for simpler shapes).
1. Preparing Your Model
Your model is the original form that you'll create a mold from. It can be made from various materials, including wax, clay, wood, or even a 3D-printed object. Ensure your model is clean, smooth, and free of imperfections. Imperfections will be replicated in your mold and final ceramic piece.
Important Considerations:
- Undercuts: If your model has undercuts (parts that are recessed and prevent easy mold removal), you'll need to make a multi-part mold.
- Draft Angle: Incorporate a slight draft angle (a gradual taper) on vertical surfaces to facilitate easy mold removal. A slight taper of 1-2 degrees is often sufficient.
2. Creating the Mother Mold (the outer mold)
This mold will contain the plaster that forms the mold for your ceramic piece. You'll need a suitable container, slightly larger than your model, to act as a mold box.
- Lubrication: Thoroughly coat the inside of the mold box with a suitable mold release agent, such as petroleum jelly or a commercial mold release. This prevents the plaster from sticking.
- Plaster Mixing: Mix the plaster according to the manufacturer's instructions. The consistency should be creamy but not too runny.
- Pouring: Carefully pour the plaster into the mold box, ensuring it completely surrounds your model.
- Setting: Allow the plaster to set completely, usually for several hours. The setting time will vary depending on the type of plaster and the ambient temperature.
3. Creating the Working Mold (the inner mold)
Once the mother mold is fully set, you can create the working mold, which will directly interact with the slip.
- Separation: Carefully remove the model from the mother mold.
- Lubrication: Apply a mold release agent to the model and inside the mother mold.
- Plaster Mixing: Prepare a fresh batch of plaster.
- Pouring: Pour the plaster into the mother mold, completely covering the model.
- Setting: Allow the plaster to set completely.
4. Separating the Molds and Finishing
Once set, carefully separate the mother mold and the working mold. You now have a two-piece mold ready for slip casting.
Finishing Touches:
- Smooth the edges: Smooth any rough edges on the working mold.
- Seal the mold: Consider sealing the mold with a suitable sealant to improve its durability and prevent water absorption from becoming too rapid.
Tips for Success
- Practice: Practice makes perfect! Start with simple shapes before attempting intricate designs.
- Cleanliness: Maintain cleanliness throughout the process to avoid imperfections in the final cast.
- Experimentation: Experiment with different plaster types and mold release agents to find what works best for your needs.
By following these steps, you'll be well on your way to creating high-quality slip-casting molds for your ceramic projects. Remember, patience and attention to detail are key to successful slip casting.
Featured Posts
Also read the following articles
Article Title | Date |
---|---|
How To Sharpen Hook Knife | Mar 13, 2025 |
How To Protect Yourself As A Man In A Divorce | Mar 13, 2025 |
How To Start A Pilates Studio | Mar 13, 2025 |
How To Make A Flesh Light With A Condom | Mar 13, 2025 |
How To Replace Crankshaft Seal | Mar 13, 2025 |
Latest Posts
Thank you for visiting our website which covers about How To Make A Mold For Slip Casting . We hope the information provided has been useful to you. Feel free to contact us if you have any questions or need further assistance. See you next time and don't miss to bookmark.